Implementation of 5S to DSG work areas group wide
5S is a five-step methodology for creating a more organised and productive workspace: Sort, Set In Order, Shine, Standardise, and Sustain.
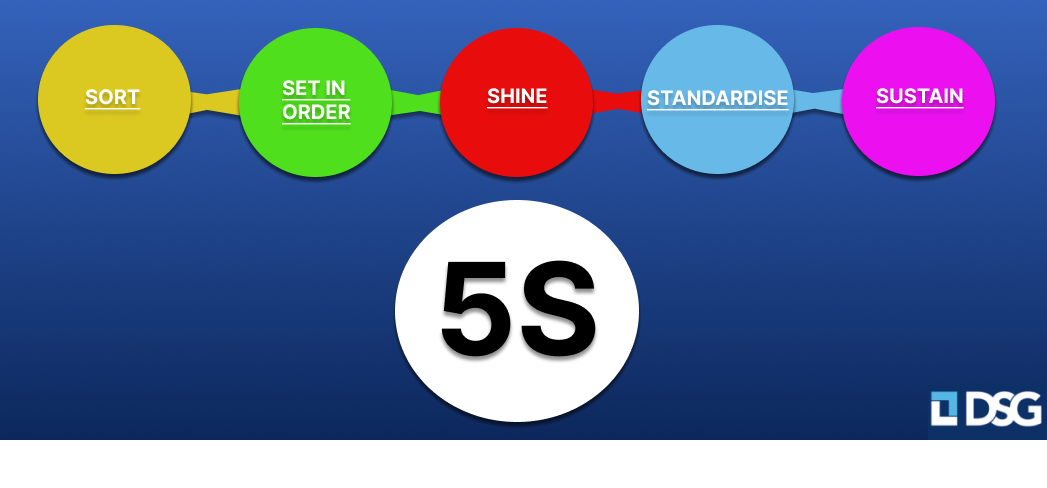
Introduction
Implemented by Ray Eagle, Director of Health and Safety at Doyle Shipping Group, the LEAN 5S program is a methodology which results in a workplace that is clean, uncluttered, safe, and well organised.
5S helps reduce waste and optimise productivity. The need for this program stemmed from a necessity to optimise processes and keep in line with the company’s value of Kaizen - continuous improvement. Thus, on the 23 of February 2022, it was announced that 5S was to be implemented group wide across all DSG sites, lead by DSG 5S Champion – Robyn Leech.
What is 5S?
5S is a LEAN management tool, originally developed in Japan, and made famous by Toyota Manufacturing division that helped take the Toyota brand global.
In today’s competitive environment, companies are fueling growth through LEAN operations. Adopting LEAN practices focuses on eliminating waste in business processes, create cost savings while establishing an environment of continuous improvement. The role of 5S as a LEAN principle is to develop a quality work environment both physically and mentally.
5S operates on 5 pillars - or steps – that are used to create a workplace suited for visual control and lean production.
The 5 pillars of 5S are:
Sort: To physically sort all items in each work area and systematically remove and discard items that are not needed in the workplace, including excessive stock of any items.
Set in order: To organise and arrange necessary items in a neat and systematic manner so that they can be easily retrieved for use and to return to their dedicated storage areas after each use.
Shine: To physically clean and inspect the workplace, including work spaces, plant, machinery, and equipment thoroughly so that there is no dirt, trash, or rubbish on or inside of workspaces.
Standardise: To maintain a high standard of workplace organisation by always keeping everything clean and orderly and everything in its dedicated storage location.
Sustain: To train people to practice the 5S system continuously so that it becomes habitual and ingrained in the culture of the organization.
Why is 5S being implemented?
5S is a straight forward methodology, driven by logical, natural human behaviour. When you adopt 5S thinking, you put safety, organisation and effectiveness ahead of production deadlines, profits, and output.
The benefits of implementing 5S include (but are not limited to) the following:
· Less Waste (Improved Efficiency).
· Reduced Space Used For Storage.
· Improved Maintenance.
· Improved Safety.
· More Committed Employees.
· Improved Quality.
5S Implementation
Since starting the rollout of 5S group wide in February 2022, our sites in Dublin, Greenore, Foynes and, Cork have begun implementing 5S throughout all their work areas and are continuing to make the developments and progress in 5S Implementation. Below you can see an example of “before” and “after” images from the implementation of 5S.
.png)
On the 18 of November 2022, Foynes became our first site to successfully complete 5S implementation throughout all work areas. Attached is an example of the "before" and "after" of the implementation of 5S in Foynes, where a peace of machinery was given as designated place for parking before and after use. Thus keeping in line with the 5S saying, "a place for everything and everything in its place".
.png)
Conclusion
For the DSG sites that have completed 5S, the work is not over!
Sustain is a constant process in 5S that needs to be consciously managed and improved. The way in which this is managed is to make sure all employees are aware of, and practice 5S daily and remain focused on the 5S program. Furthermore, management is involved in checking work areas, ensuring that employees are adhering to 5S standards through regular reviews and site audits. 5S will continue to be implemented throughout all DSG sites in 2023.